Many manufacturers fail when they attempt Continuous Improvement (CI) initiatives without an aligned MOM system strategy. Many manufacturers attempt MOM systems without an aligned CI initiative and fail. As a result, a new global industrial revolution has begun based on how to optimize manufacturing plants by combining CI methods with an adaptive MOM system architecture put into place using a Manufacturing Transformation Strategy. Though manufacturers are still transforming raw materials into valuable products, their needs have evolved.
Maturity models help to create a shared vision of process improvement within the organization and to set priorities based on objective measurements.
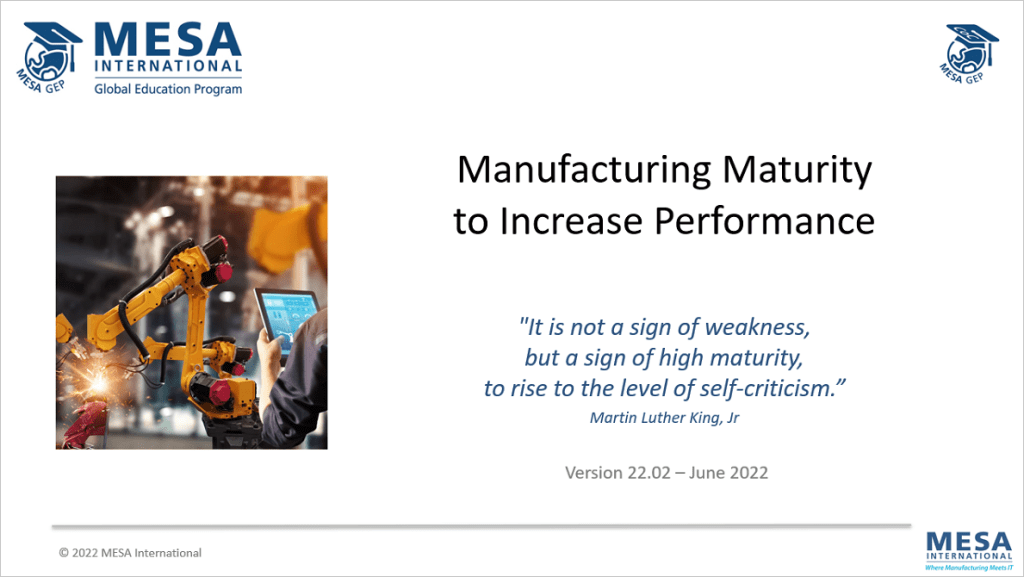
This module explains how to use ISA-95 to assess the current state and as a tool to design a future, improved way of working. A maturity capability assessment delivers the current maturity level and provides guidelines for structured step-by-step improvement via a plan.
In the roadmap, each MOM project ROI identifies corrective actions to mitigate risks through required change to organization structure, process, personnel and technology. Traditionally, industrial companies view manufacturing cost reduction as only a labor cost issue. Often, it is not even the biggest cost factor. Significant cost reduction is a matter of effective work processes across plants and supply chain operations for normal and abnormal operating states. The real solution for effective work processes requires simultaneous changes in organization structure, operations processes, and employee skill sets all enabled by MOM technologies.
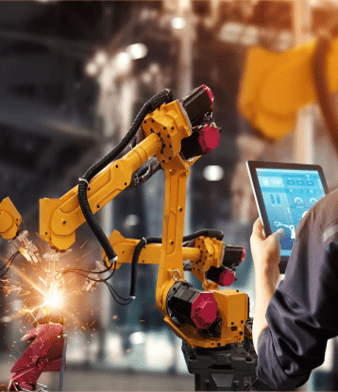
|