Bringing more automation to the shop floor eventually makes the shop floor more dependent on IT. IT systems provide the data to start production, or during production data is to be collected and recorded. An IT system downtime event or an interface that misbehaves brings questions such as;
- “How much system downtime do we accept if we cannot change over to the next production order?”
- “If we cannot collect data from our operations and we cannot get evidence of production quality, how long does it make sense to continue production operations?”
As a result of more connectivity, there will be higher uptime requirements for shop floor IT systems. This not only impacts the IT systems (bringing in high availability / redundancy solutions) but also the support organization. Support for shop floor IT traditionally resides close to OT organization in the site, close to the production shift and the maintenance department. IT system integration requires the OT organisation to connect to the IT domain, as integration gives a different set of complications and a wider scope of possible root causes. It requires more IT expertise and a broader focus. The little issue in the PLC that often can be resolved locally on the spot, is a different issue compared to a connectivity issue between MES and ERP.
To handle this change;
- the traditional OT department needs orientation to IT with IT skills and knowledge
- the IT department in return requires an OT orientation, understanding the 24/7 production calendar, the urgencies behind a stopped production line, and awareness on critical elements in the IT network for uptime and shop floor continuity
Much has been said about connecting IT and OT worlds and it deserves attention for sure: to bring these different worlds together is a precondition for digital on the shop floor. And it may require a discussion on the C-level, as OT is by its origin often a responsibility for the COO, where IT is in the hands of a CIO or CFO.
A good way to align and connect IT and OT worlds is to form a Manufacturing group on corporate level, like a competence group. On the one hand there is representation from Operations, setting out the course, defining priorities, solutions and support the continuous improvement in the sites. Or alternatively IT is represented there for support and guidelines for and contacts to local OT.
Discover how MOMi’s Standard Business Consultancy Services can change your manufacturing operations.
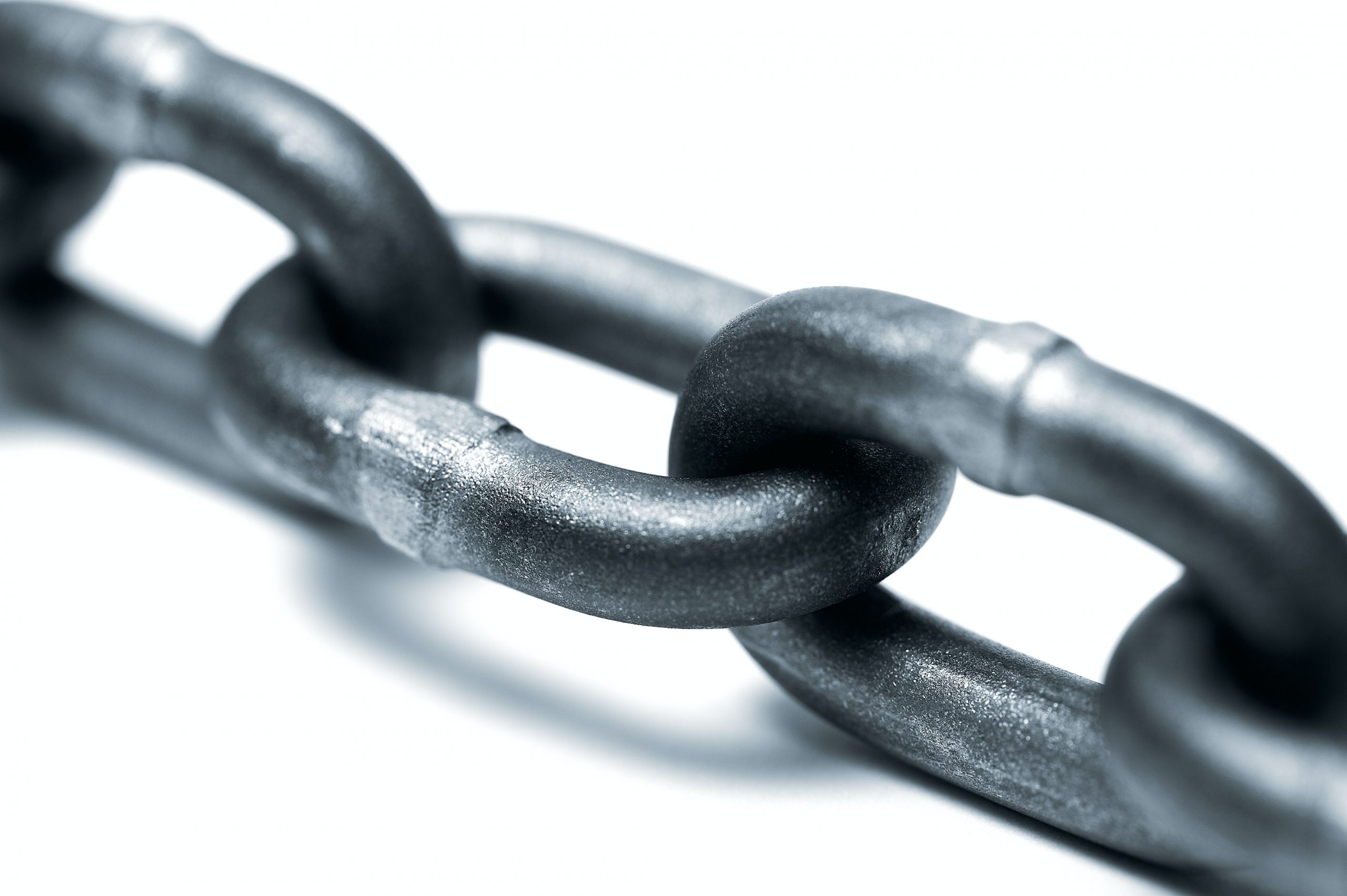